Linde X20-35

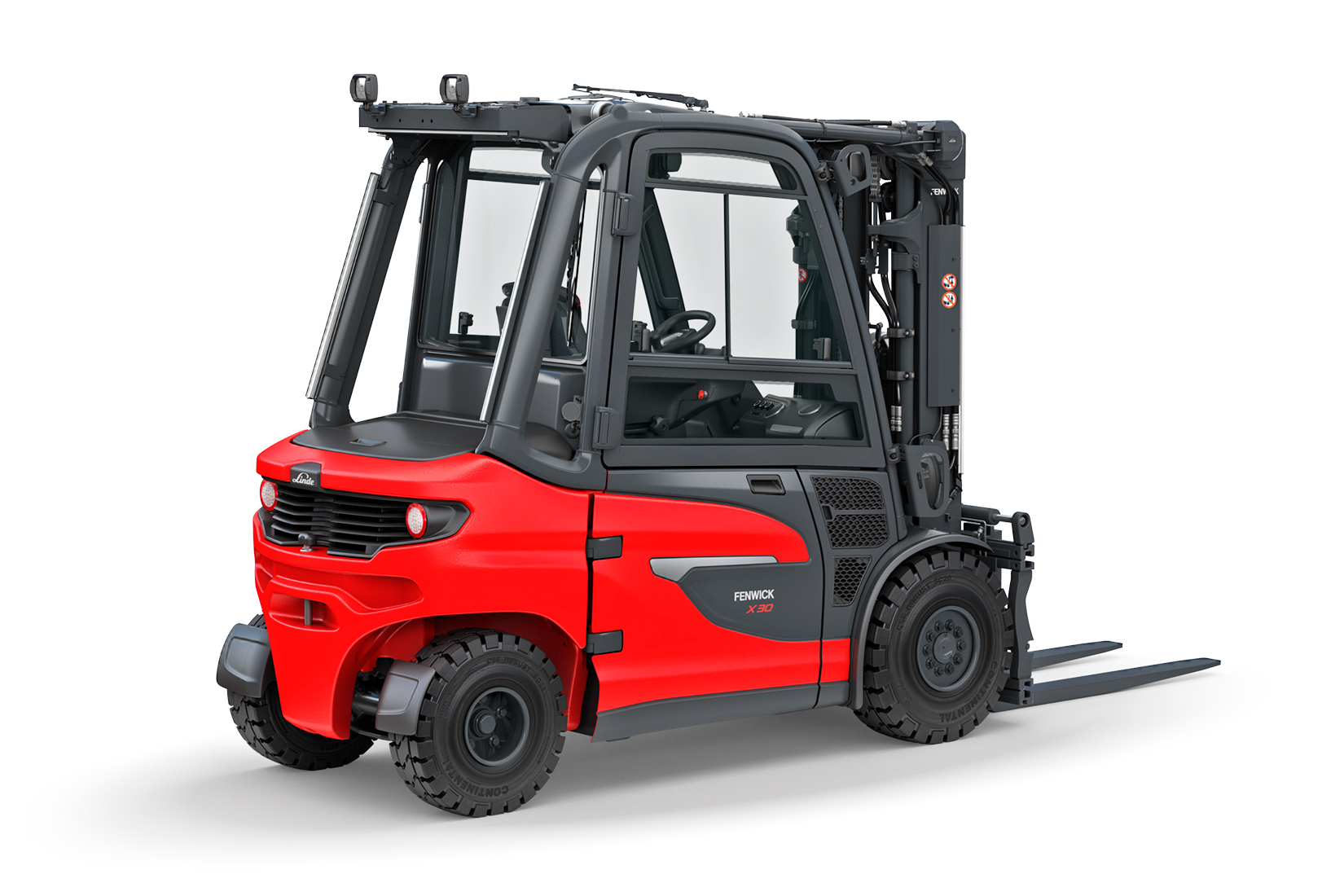
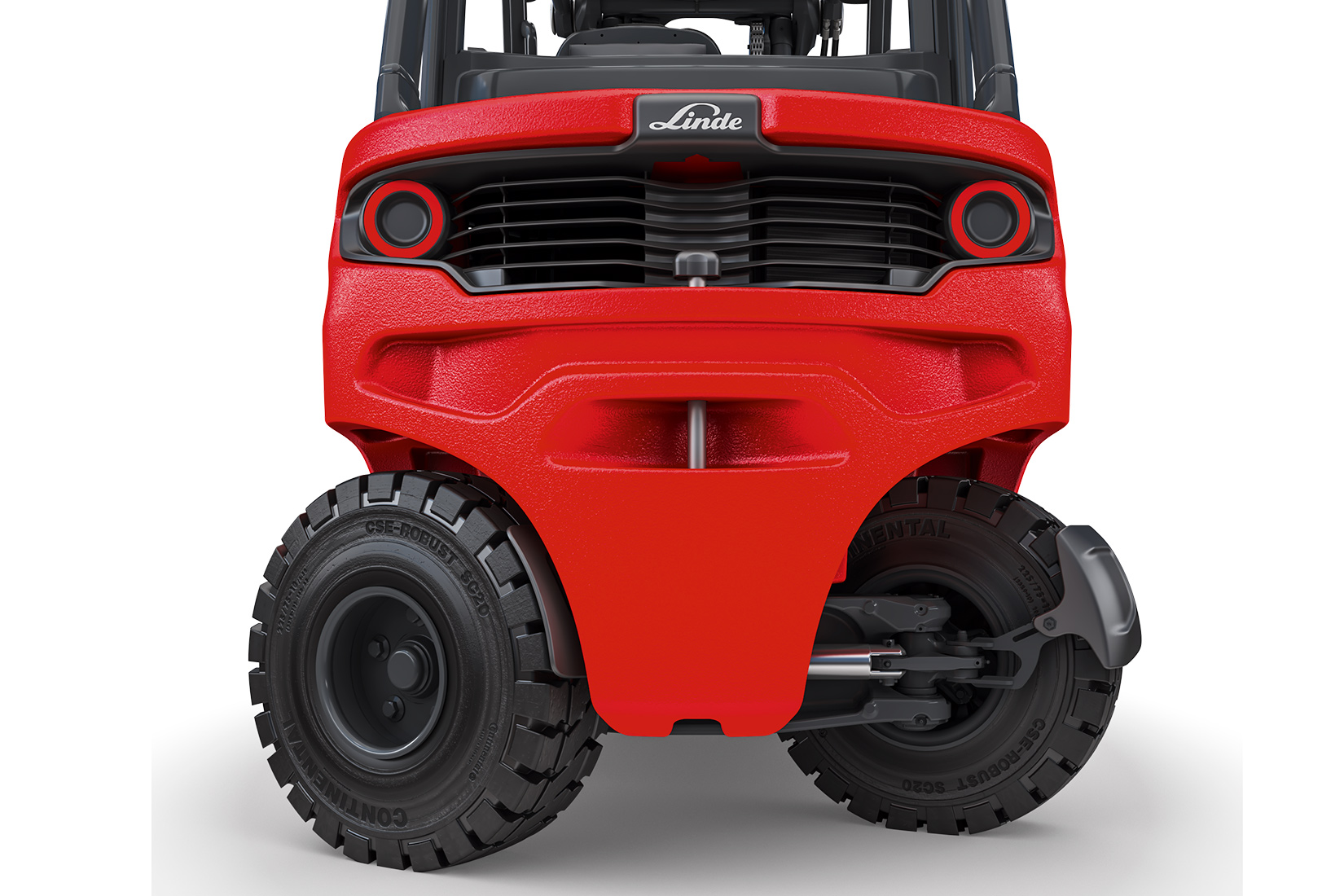
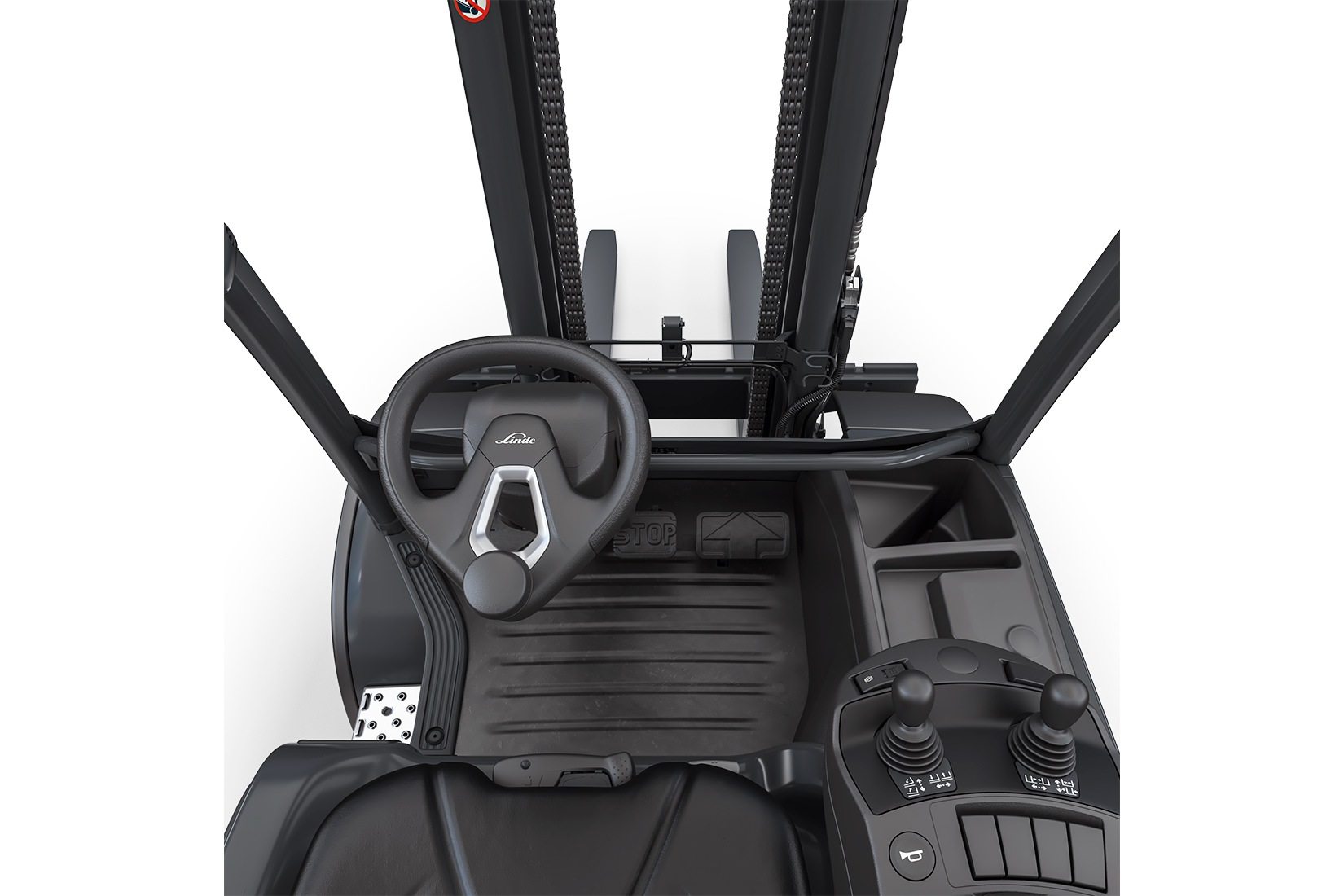
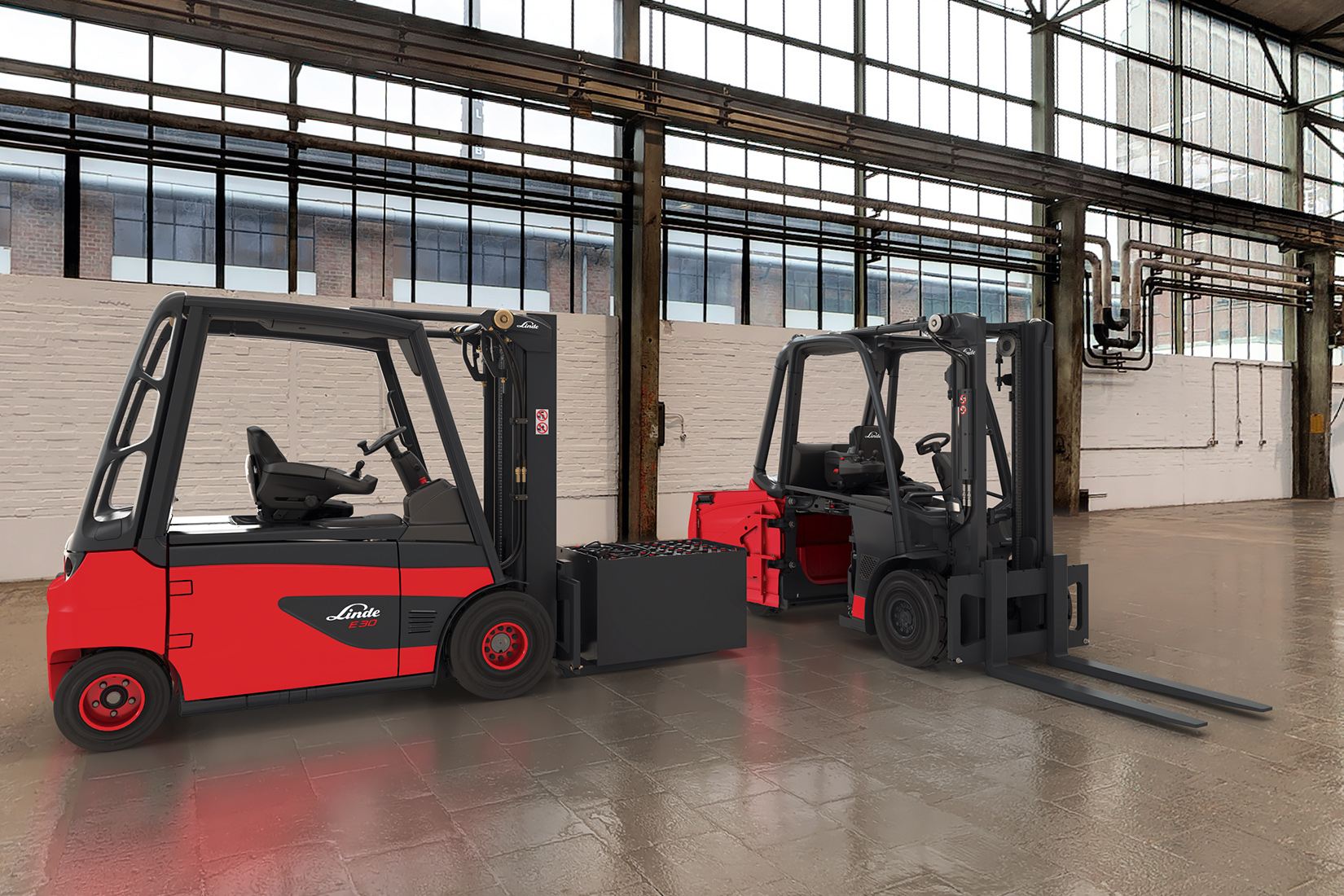
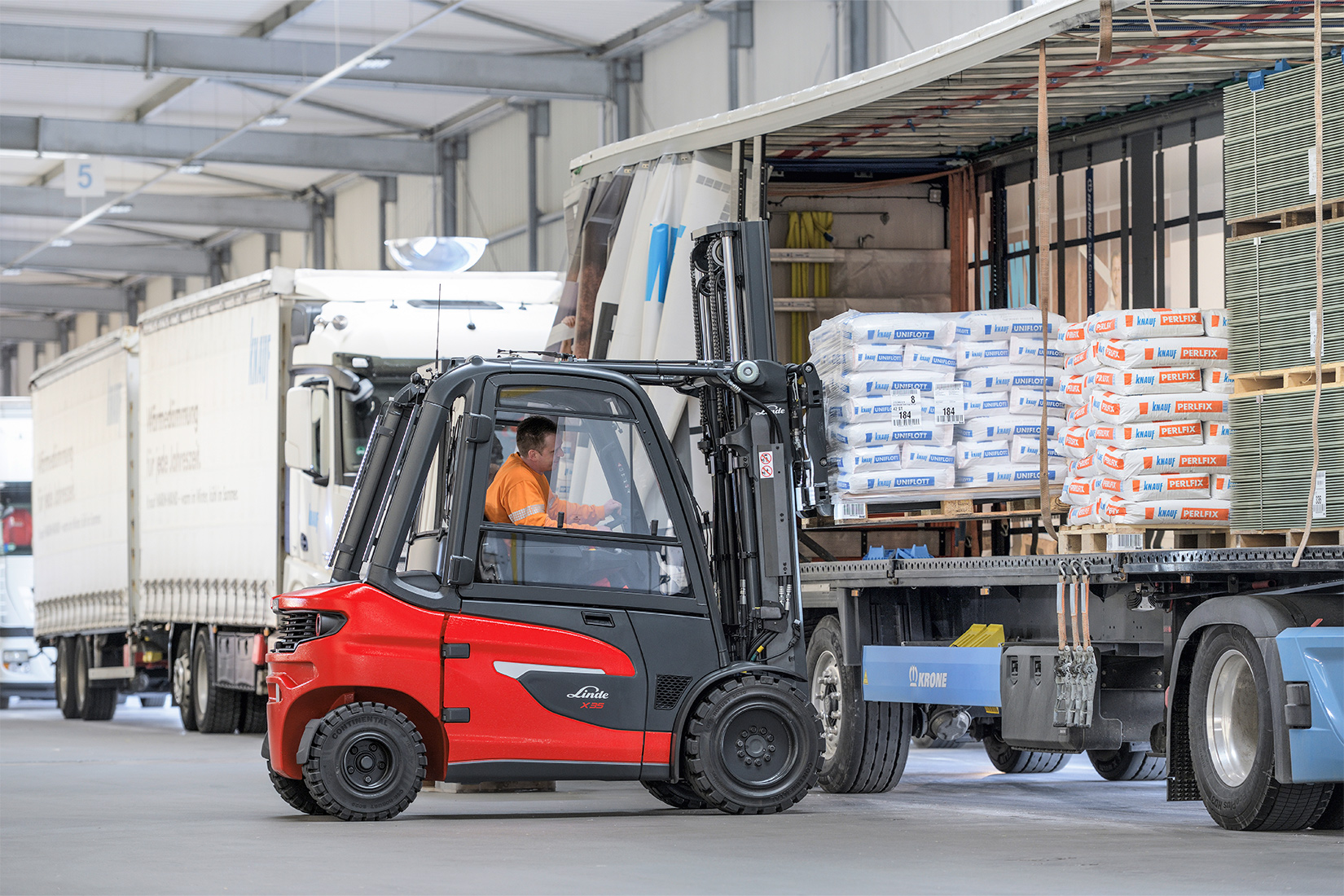
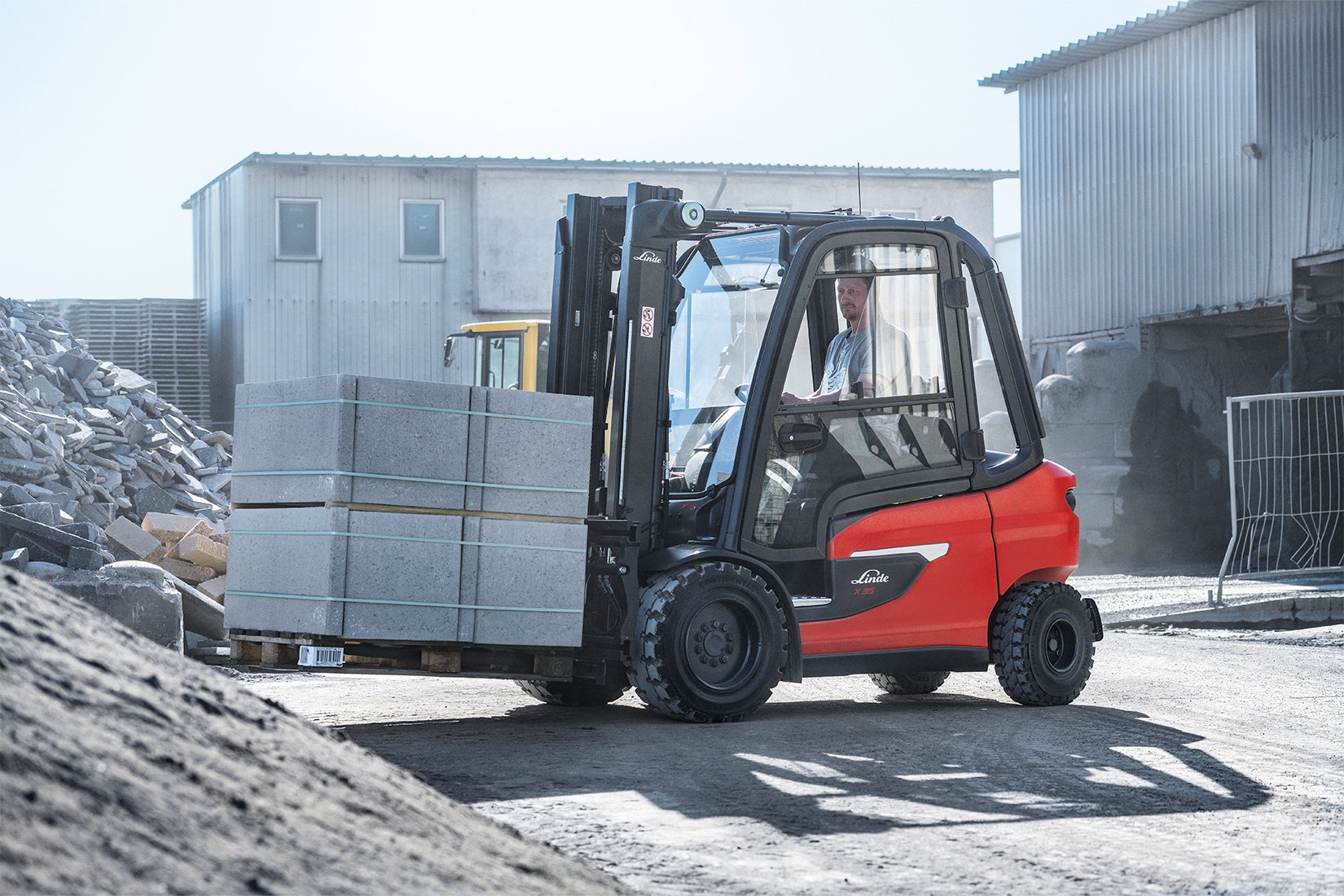
The X20 – X35 counterbalance forklift trucks from Linde Material Handling are the first electric forklifts whose high performance and robustness means they can be used as a genuine alternative to internal combustion (IC) trucks.
The X20 – X35 counterbalance forklift trucks from Linde Material Handling are the first electric forklifts whose high performance and robustness means they can be used as a genuine alternative to internal combustion (IC) trucks.
The X20 – X35 counterbalance forklift trucks from Linde Material Handling are the first electric forklifts whose high performance and robustness means they can be used as a genuine alternative to internal combustion (IC) trucks. Customers therefore enjoy absolute freedom of choice and are able to choose a quiet, emission-free alternative for even the most challenging applications, without having to allow for any loss of performance. The basis for all of this is the common platform developed by Linde for counterbalance forklift trucks, whether powered by internal combustion engines or electricity. This means that the X20 – X35 forklifts combine the best of two worlds: the characteristic output and power development of IC trucks and the dynamics, flexibility, and freedom from emissions offered by electric trucks.
The comprehensive safety concept of the X20 – X35 electric forklift trucks protects not only the driver but also pedestrians and the goods being transported. The slimline mast design, narrow A-pillar, and lowered front plate afford the driver an unimpeded view of the load and surrounding area. Even when loading and unloading at higher levels, the roof design continues to give the driver a perfect view of the load. The truck’s low center of gravity and high steering axle ensure a high degree of protection from the risk of overturning. In addition, Linde Curve Assist, fitted as standard, reduces truck speed on bends and prevents it from tipping over. If the load is tilted too far forward when lifting, the Linde Load Assist, which is integrated as standard, automatically intervenes to reduce the forward tilt and lifting speed according to the lifting height. This function minimizes the risk of accidents caused by falling loads.
The spacious and comfortable workspace for the driver and the ergonomic seat versions ensure an optimal operating experience and combat tension and exhaustion. Thanks to the wide field of view, the driver can easily keep both the load and the surrounding area in sight at all times. The truck functions can be operated with little physical effort since all of the central control elements are close at hand around the driver. Even on uneven floors, the ride is comfortable and even. The chassis is separate from the drive axle through an elastomer ring bearing and from the mast and steering axle by additional bearings, so the driver feels significantly less vibration and jolting. This also reduces noise, causing less overall physical strain on the driver and contributing to higher handling capacities.
As the new electric high performers, the X20 – X35 forklifts can be used for the most demanding applications, even on uneven floor surfaces. This is made possible by the wheelbase, which is long for an electric forklift, and the large tires, together with the vibration-free drive axle. Neither dust and dirt nor steep ramps, long distances or regular heavy loads and high lifting will push these new electric forklift trucks to their limits. The key to all of this is the new synchronous reluctance motor with permanent magnets (SRM+), together with an innovative water cooling system that keeps the power modules within the ideal temperature range. This ensures a consistently high performance even in extremely demanding multi-shift operation. In addition, the top-mounted tilt cylinder, in combination with the torsion-resistant mast design, offers a high residual load capacity and safe handling of loads of between 2–3.5 tonnes, even at considerable lifting heights.
The driver can view all of the important information—such as remaining battery levels, warning lights, and operating hours—at a glance from the 3.5-inch display, fitted as standard. Text information on the display guides the driver through simple maintenance processes. Firmware updates and fault diagnosis can be carried out remotely. This reduces the number of service operations and hence reduces servicing costs. Service and repair intervals are calculated on the basis of constantly updated operating hours. Wear and any damage that occurs are identified at an early stage by remote diagnosis. The temperature sensor integrated as standard, which continuously analyses measurements such as oil temperature in relation to ambient temperature, is one of the elements that makes this possible. Serious consequential damage is thus avoided. The mast and driver’s workspace are modular assemblies that can be replaced quickly and easily, reducing the downtime required for repairs.
Linde has developed a new interface: the Multifunction Lever. It makes operating Linde reach trucks and forklift trucks in the 12xx-series effortless and perfect human machine interface.
The radar-based system detects any moving or static object/person behind the forklift and actively slows down with the highest deceleration level possible across the industry.
An intelligent camera solution that can, in real-time, distinguish between people and other objects within the machine's workspace. The operator is gradually alerted both visually and acoustically based on the machine's proximity to a person.
The conventional steering wheel in front of the operator has been replaced with a mini-wheel or a joystick on the armrest. Behind this innovative new design from Linde is many hours of intensive R&D work.
The system warns the operator if the wheel steering angle exceeds 25 degrees. The warning can be a visual alert, a visual and acoustic alert, or a visual and acoustic alert including a speed reduction to creep speed. The function is configured by the service technician.
Advantages:
Note: The system is only active upon the initial start-up of the truck.
Linde has developed a new interface: the Multifunction Lever. It makes operating Linde reach trucks and forklift trucks in the 12xx-series effortless and perfect human machine interface.
The radar-based system detects any moving or static object/person behind the forklift and actively slows down with the highest deceleration level possible across the industry.
An intelligent camera solution that can, in real-time, distinguish between people and other objects within the machine's workspace. The operator is gradually alerted both visually and acoustically based on the machine's proximity to a person.
The conventional steering wheel in front of the operator has been replaced with a mini-wheel or a joystick on the armrest. Behind this innovative new design from Linde is many hours of intensive R&D work.
The system warns the operator if the wheel steering angle exceeds 25 degrees. The warning can be a visual alert, a visual and acoustic alert, or a visual and acoustic alert including a speed reduction to creep speed. The function is configured by the service technician.
Advantages:
Note: The system is only active upon the initial start-up of the truck.
Fill out the form below and we will send you sales material on the desired machines.